ボトルネックの解消で
生産性をアップ
製造業のDXを支える【ローカルDXシステム】
製造業において、生産性の向上は競争力を維持するために不可欠です。「ローカルDXシステム」は、生産ラインのボトルネックを特定することができ、効率的な改善ができる強力なツールです。
ボトルネックの見える化→ボトルネックの対策→ボトルネックの解消→次のボトルネックが見える→ボトルネックの対策を繰り返すことで無理なく生産性の大幅なアップが可能となります。
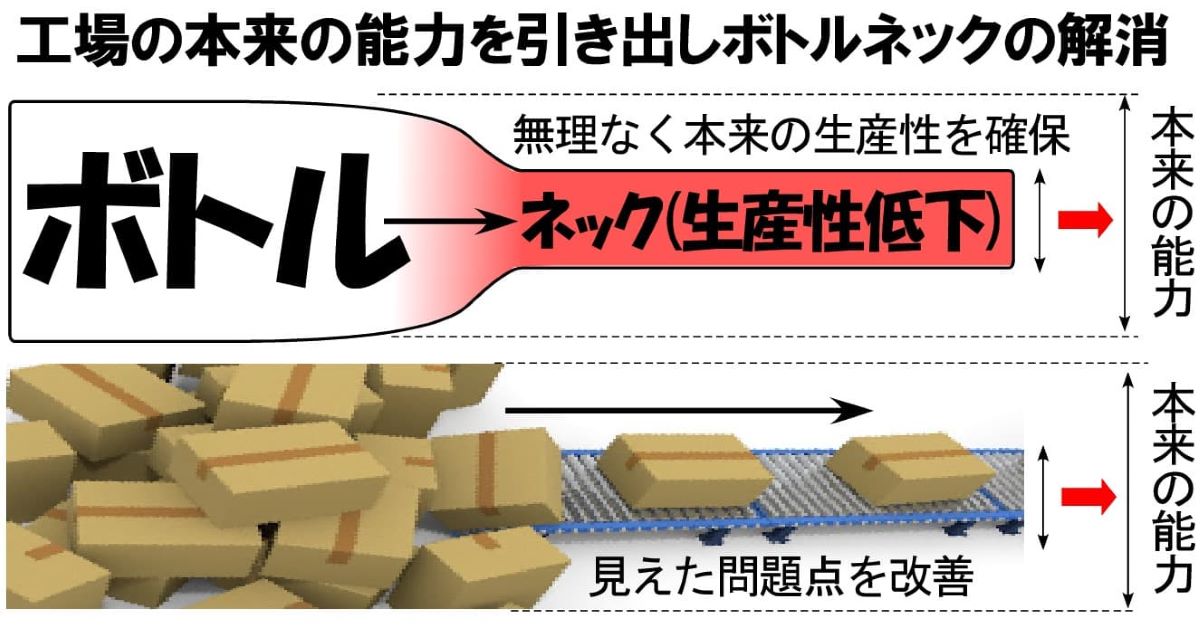
ボトルネック解消の概要
ローカルDXシステムの機能として、基本の稼働関連のデータの視点を変えた活用や個々の加工工程に合わせたセンサの活用でボトルネックの表示、管理ができます。
具体的には各工程の直近一定時間の各機械の加工数や加工時間、加工量などのデータを移動平均のグラフで作業や加工の流れの順に配置します。
基本は各種のデータをリアルタイムに見える化して特異な問題点を抽出し、改善することにより生産性を向上させます。
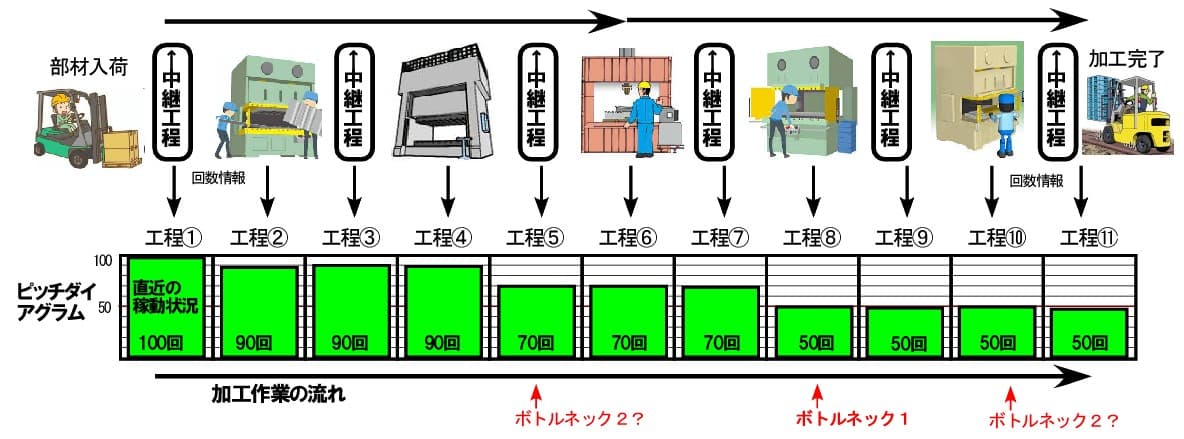
- それぞれの工程が順調な場合、各グラフの高さはほぼ一定になり、問題が発生するとそれ以降の高さは下がります
- ボトルネック解消でそのポイントが分かり難い場合、その工程に更にセンサを追加して濃い情報の収集ができます
- 上図で「ボトルネック1」がわかればそれを改善することで次の「ボトルネック2」が浮かび上がります
- 全体に生産性が低い場合、ボトルネックは現れないためその場合、加工の最上流から対策をとる必要があります
ライン全体の可視化と改善
ピッチダイアグラム
ピッチダイアグラムとは、生産ラインのバランスを可視化するためにグラフを用いてバランス分析を行う方法です。グラフの縦軸に工程ごとの作業時間を並べ、横軸に工程や作業者を並べるように作ります。
- 各ステーションの作業サイクルを可視化でき、生産効率の最適化ができます
- 各工程の作業時間を明確に把握でき、全体の工程の改善が容易になります
- どの工程が生産全体の効率を低下させているか等の改善場所が把握できます
- ムダな待機時間や生産の停滞を減少させることで、生産性のアップができます
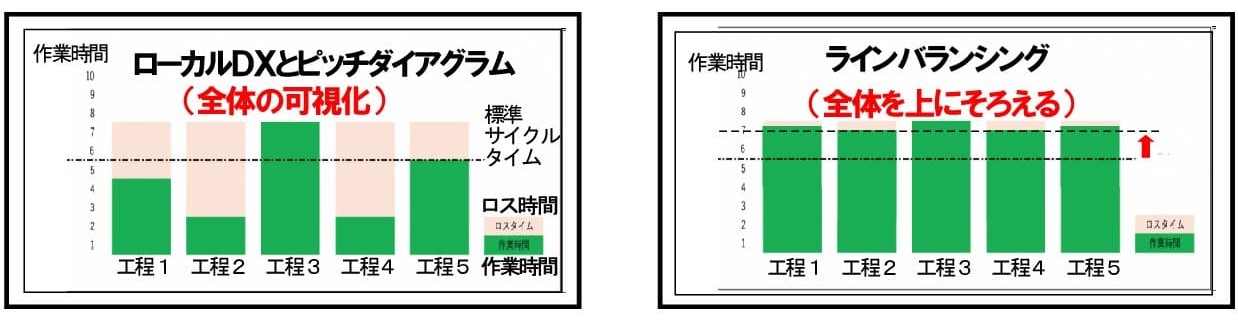
ラインバランシング
- これは生産ライン内の各工程に負荷を均等に割り振るプロセスです
- 各工程が均等に作業を行い特定の工程で作業を滞ることを無くします
- 各工程の作業を最適に配分して生産全体のリードタイムを短縮します
- 効率的なラインバランシングで作業者や稼働時間を最適化しコストを削減します
ボトルネックの改善のステップ
①現状のデータ収集と分析
サイクルタイムの把握、スループットの確認、生産ライン全体で1時間/1日あたりの生産量、各工程間の仕掛品の対流量の把握
➁ボトルネックの特定
ローカルDXシステムの標準機能のピッチダイアグラムにより、各工程の作業時間や生産数等を確認してネックの工程を特定
③原因の分析
ボトルネックの原因を人的要因、機械設備的な問題、材料や供給の問題、工程設計や工程間の不均衡、作業の流れムダ等を分析
④改善策の立案と実施
原因を明確にした後、改善策を立案し実行、ボトルネックの工程の機械の高速化やメンテナンスの強化、作業手順の改善等を見直す
⑤効果のモニタリング
改善策を実施した後、その効果をモニタリングし、スループットやサイクルタイムが改善されたかどうかを確認
⑥継続的なデータ収集
改善後も継続的にデータを収集し、新たなボトルネックや問題が発生していないかをチェックして改善の効果や追加の課題を確認
⑦PDCAサイクルでの継続的な改善
ボトルネック改善は一度ではなく、継続的にPDCAサイクル(Plan-Do-Check-Act)を用いて、常に生産ラインの最適化に努める
設置が非常にシンプルな「ローカルDXシステム」はすぐに①➁⑤⑥を可能にします
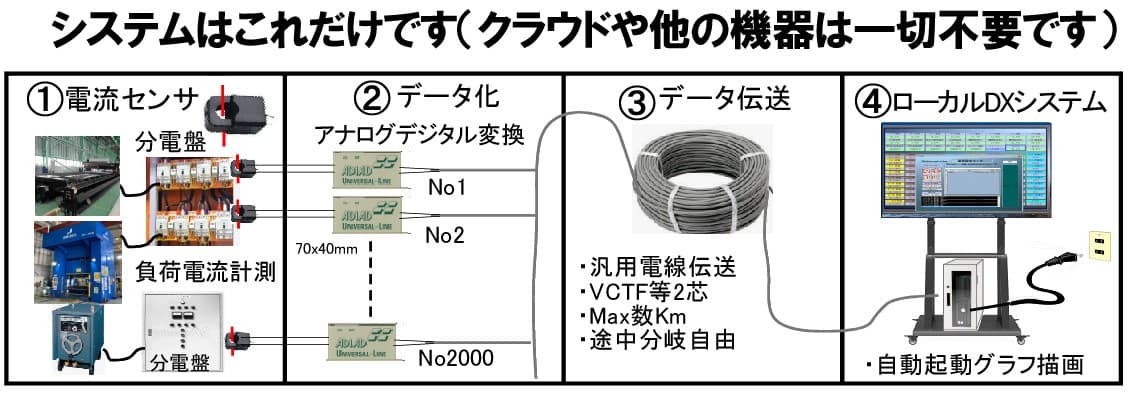
ボトルネックの解消の波及効果
ボトルネック解消の一番の目的は「稼働率のUP」ですが、それ以外にも長期的な大きなメリットがあります。大きな波及効果があり、それぞれの分野でプラスα になり、生産性向上に大きく寄与します。
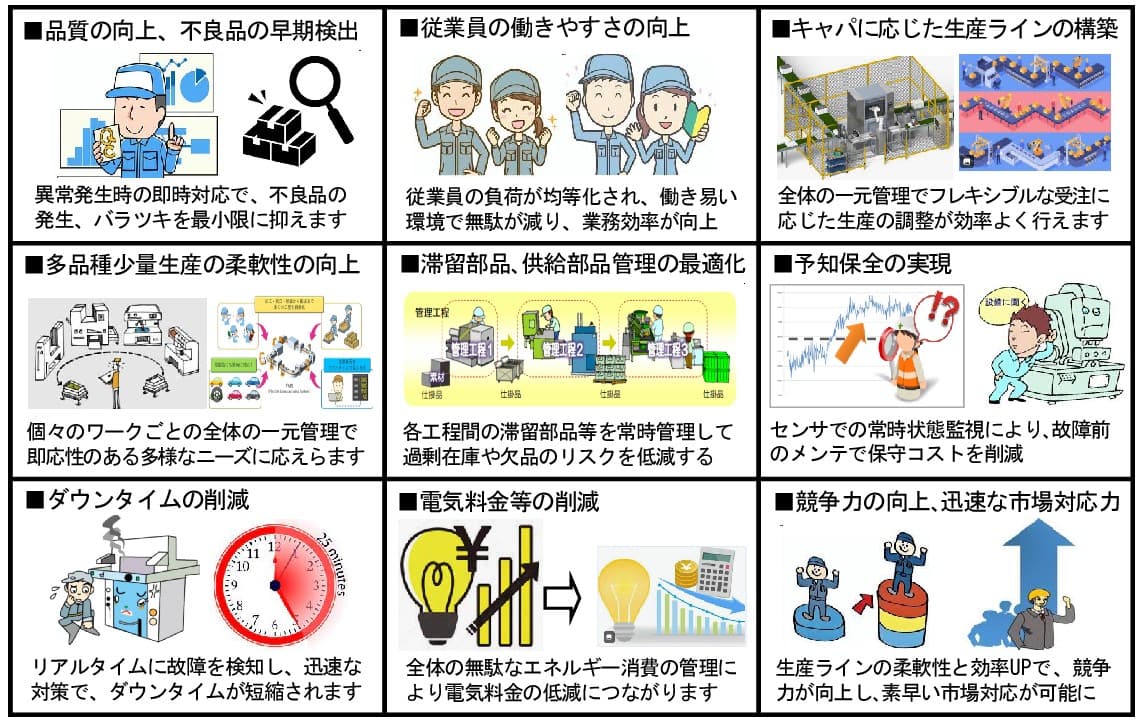
ボトルネックの解消で 現場のモチベーションUP
ボトルネック解消に貢献した従業員やチームに報奨金や特別な休暇などのインセンティブを提供して、更なるPDCAの改善ループの促進により、長期的なモチベーションのアップが継続できます。現場のモチベーションアップは更なる生産性向上につながります。
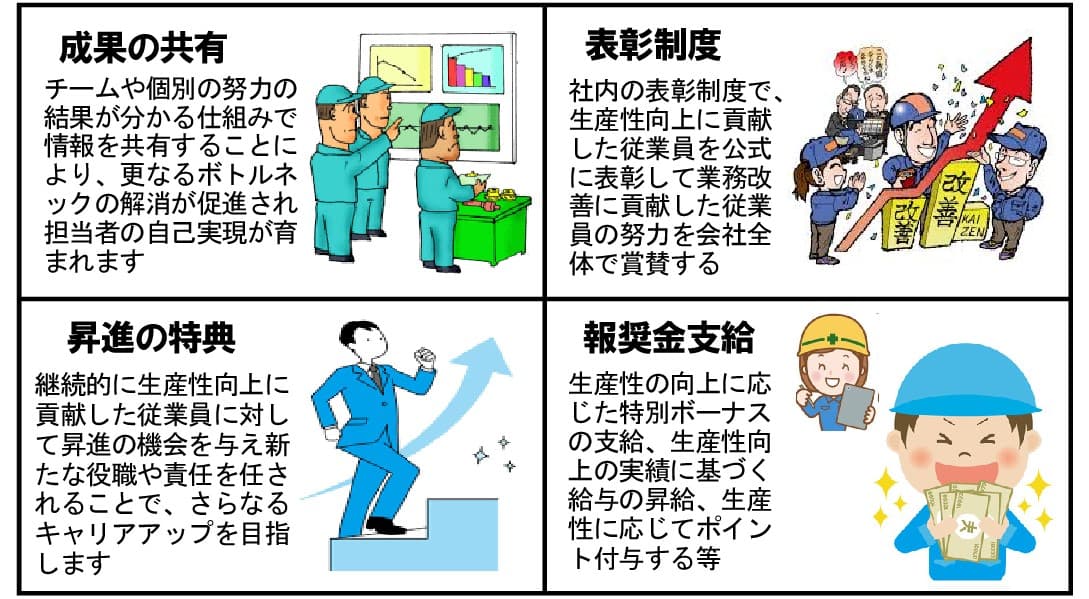
フィードバックとコミュニケーションの強化 で更なるボトルネックの解消
フィードバックとコミュニケーションの強化で更なるボトルネックの解消ができ、10%、20%の生産性UPも夢ではありません。
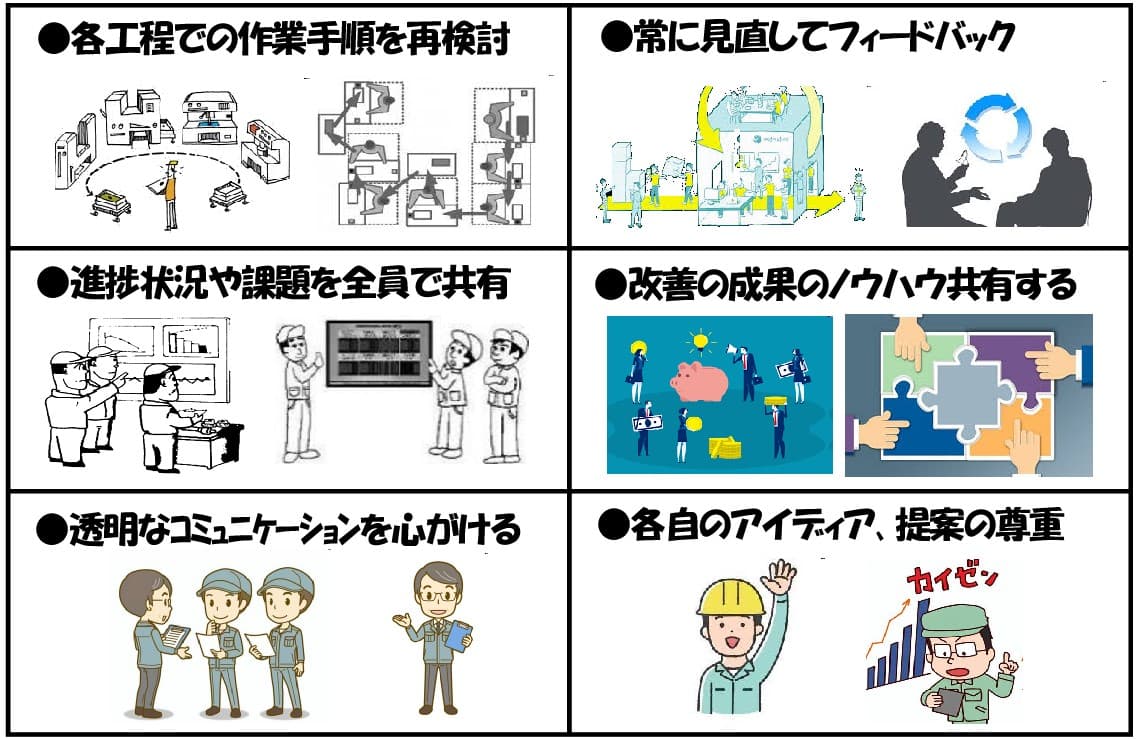
DX関連資料
▼下記をクリックしてご覧ください(PDF)▼
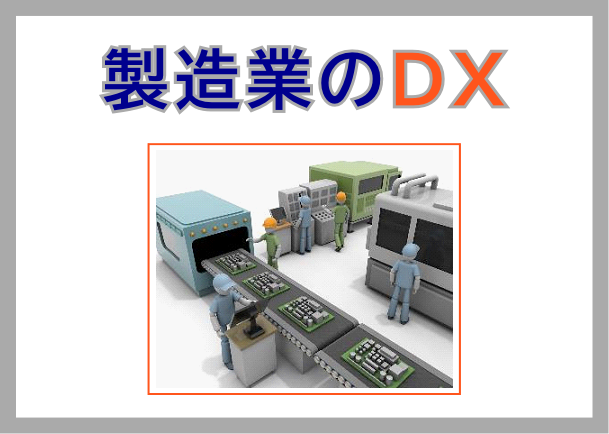
DX関連ページ
(1320)